Home
Overview
Products
Services
Site
Contents Contact
Us |
|
|
|
|
|
|
|
|
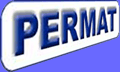
Product
Pages
Honing
Superfinishing
Centreless
Through-Feed
Machines for Cylindrical
Components
Centreless
Through-Feed
Machines for Tapered
Components
Centreless
Through-Feed
Machine with Automatic Response to Lift and
Lower the Stones at the
Interruptions
Centreless
Plunge-Cut
Machine for Cylindrical
Components
Centreless
Plunge-Cut
Machine for Taper Rollers
Further
Superfinishing
Machine Series
Tape
Finishing Machines
Deep
Hole Drilling Machines
Assembly
& Leak Testing Machines
Leak
Testing Machines
Services
|
|
|
|
|
|

Click
to enlarge
|
|
|
Superfinishing
PERMAT
supplies superfishing machines, superfinishing attachments and superfinishing
stones.
Click
on the image opposite to see an enlarged view.
|
|
|
|
|
 |
|
|
|
|
|
|
|

Stock
Removal
Stock removal is approx 5-8 µm
in Ø
Guide Value: Stock removal in
Ø = 3 to 4.Rz
resp. 15 TO 20.Ra
Results
Improvement in Roundness
Approx. 50-80% with polygons;
R-r = 0.2 µm
achievable
Advantage: Reduction of noise with anti-friction bearings and sliding
bearings High Surface Finish Rz = 0.15-0.25 µm;
Ra = 0.015-0.02 µm
Advantage: High percentage contact
area tpi 0.1 - 80-90% results in a
high load capability and reduction
of wear.
Adapted
Stock Removal
at low temperatures and low pressures.
|
|
|
What
is Superfinishing?
Superfinishing is used when grinding alone is not sufficient, or is too expensive,
to achieve a required roundness and surface finish.
The required
finish is achieved by pressing a fine-grained superfinishing stone against
the revolving component. At the same time, it is brought back parallel to
the machining surface for oscillation, while it moves in short longitudinal
strokes.
The oscillation
movement is produced electro-mechanically or by compressed air (contact pressure
is normally made by compressed air). Hardness and grain of the superfinishing
stones are selected to suit the job requirement.
Applications
Examples of use include for highly loaded bearing surfaces and sliding surfaces,
anti-friction bearing elements and friction bearing shafts, contact areas
of sealing rings and collars.
|
|
|
 |
|
|
|
|
|
|
|

SCD
80 / SCD 200
click to enlarge
Features
(SCD80 / SCD 200):
Pneumatic oscillation system
with 2400-2800 double strokes/min
Additional stroke = superimposed oscillation with 30-60 double strokes/min
Pneumatic stone contact
pressure
Hyperbolic
feed rollers - position reversible
Device to adjust angle of
inclination
Roller drive: Pole change motor - infinitely variable friction cone gear
Split bearing arrangement for
roller type* allows rapid roller
change
Height adjustment of the
oscillation head by means of push-button with gear motor and friction
clutch
Rapid adjustment of the roller distance against adjustable stops.
|
|
|
Centreless
Through-Feed Machines for Cylindrical Components
The range available includes:
Through-Feed
Machine SCD 80
Range of Application:
1.5-80 mm dia.
below 1.5 mm dia. (Upon request)
Beyond 80 mm dia. (Upon request)
Stone Guides:
7 with standard design
8 with special design
Through-Feed
Machine SCD 200
Range of Application:
1.5-200 mm Ø
Stone guides: max. 10
Features: See SCD 80
Feed Roller for Cylindrical and Crowned Machining
Example: Machining of the cylindrical centre portion and the crowned ends
of cylinder rollers in one continuous operation. Depending on the requirement
up to 10 Stone guides.
Back
|
|
|
|
 |
|
|
|
|
|
|
|
 SCD
200-KE 35
click to enlarge
Features:
Basic machine SCD 200 or
SCD 80
Special equipment for taper
rollers:
Either:
Interlinkage For interlinking with the Grinding Machine
Or: Feeding and Orientation device (see picture above)
|
|
|
Centreless
Through-Feed Machines for Tapered Components
Through-Feed
Machines for Taper Rollers
Range of Application:
|
SCD
200-KE 35 |
SCD
80-KE 20 |
L (mm) |
Max. 35* |
Max. 20 |
Dia. (mm) |
approx. 4.5-25 |
approx. 4.5-12 |
a |
max. 10 |
max. 10 |
*Larger
lengths and angles upon request Back |
|
|
|
|
 |
|
|
|
|
|
 SCD
200 AS
click to enlarge
Typical application:
Shock absorbers
Features:
Basic Machine SCD 200
Special equipment:
Automatic stone response
Component feed and removal
|
|
|
Centreless
Through-Feed Machine with Automatic Response to Lift and Lower the Stones
at the Interruptions
Through-Feed
Machine SCD 200 AS
Range of Application:
7-30 mm dia.; max. 600mm length
(Differing dimensions upon request)
Stone Guides: max. 10 off
Recessed parts are machined by
the through-feed process if the diameter of the recess is smaller than the
machining diameter. Short recesses can be spanned by long stones. If the total
length of the recess is more than 50mm, and in cases where the tolerance of
the diameter is larger (more than approx. 10 µm),
automatic response to lift and lower the stones is necessary.
Back
|
|
|
|
 |
|
|
|
|
|
|
|
Left
6 SCE 80; Right
SCE 25, click to enlarge
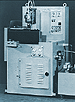
Features
(6 SCE 80):
Use of SCD 80 units
Pneumatic oscillation system with 2400-2800 double strokes/min or mechanical
oscillation system with 1450 double strokes/min when working close to shoulders
1.5mm
Additional stroke = superimposed oscillation with 30-60 double strokes/min
Pneumatic stone contact pressure
Features (SCE 25):
Oscillation system
Either: pneumatic Superfinishing Attachment SG 50 2300-2800 or
2800-3200 double strokes/min with undercut widths >1.5mm
or: electro-mechanical oscillation system with 1450 double
strokes/min for small shoulder distance or undercut widths
1.0mm >
Pneumatic stone contact
pressure
Roller bearing arrangement:
Flying or with counter bearing
Roller drive:Pole change gear
motor
Supporting unit for projecting
parts
Axial depth stop
Exchangeable rollers: Since the roller distance is not adjustable, 9 roller
pairs Are required for the diameter range 3-25mm
|
|
|
Centreless
Plunge-Cut Machine for Cylindrical Components
Plunge-Cut
Machine 6 SCE 80
Range of Application:
5-50mm dia.
Machining length max. 75mm
No. of Stations:
Max. 6
(depending on component length)
Principle: As a rule, machining
is done with only one stone in the following manner:
Rough machining at approx. 15-25 m/min
Finish machining at approx. 45-150 m/min
Plunge-Cut
Machine SCE 25
Range of Application:
3-25mm dia. Or 10-30 mm dia.
Machining length max. 60 mm
No. of Stations: 1
Back
|
|
|
|
 |
|
|
|
|
|
|
|

6
SCE 80 KE
click to enlarge
Features:
Use
of SCD 80 units
Pneumatic
oscillation system with 2400-2800 double strokes/min
Additional
stroke = superimposed oscillation with 30-60 double strokes/min
Pneumatic
stone contact pressure
Roller
drive; Pole change motor,
with cycle times under 12 sec. D.C. drive
Principle: Rough machining at
Approx. 15-25 m/min
Finish machining at approx. 45-150 m/min
|
|
|
Centreless
Plunge-Cut Machine for Taper Rollers
Plunge-Cut Machine
6 SCE 80 KE
Range of Application:
Taper rollers
D = 5-40 mm; dmin = 4 mm
Lmax. = 75 mm; @max. = 10
No. of Stations: Max.
6, depending on the length of the taper rollers
Back
|
|
|
|
 |
|
|
|
|
|
|
|

Permat
Machines Limited
Station Road, Coleshill,
Birmingham
England B46 1JG
Tel:
+44 01675 463351 Fax: 01675 465816
Telex: 336040
Nagel
Maschinen-und
Werkzeugfabric GmbH
P.O. Box 1709 D-7440 Nurtingen
Tel: 07022 605-0 Telex: 7267337
|
|
|
Further
Superfinishing Machine Series
STM
Centerless Plunge-Cut Machines With "circular arc shaped" oscillation movement
for Generating lines of spherical rollers Number of stations: either 2 or
4
SE and SEL
Machines for machining between centres or in the Chuck
Type SE for plunge-cut machining
Type SEL for plunge-cut and longitudinal machining
SG
Superfinishing Attachments e.g. for Lathes
SG 50 pneumatic, with 1 stone
guide
SG 75 pneumatic, with 2 or
3 stone guides
SGM 10 electro-mechanical,
with 1 stone guide
SGM 100 electro-mechanical,
with 4 or 6 stone Guides
SGMK 2500 transportable Calender
Superfinishing Unit for machining of rollers in the calender Column
SPH and SPV
Finishing Machines with "rotating" honing sleeves for Machining of thrust
faces and spherical faces
Type SPH, horizontal design*
Type SPV, vertical design*
*In single- and multi-spindle design
Back
to top
|
|
|
|
|
|
|
|
|
|
|
|
|
|
|
 |
 |
 |
 |
 |
 |
 |
 |
342